Just How Metal Stamping is Transforming the Automotive and Aerospace Industries
Checking Out the Globe of Metal Stamping: From Design to Production
Within the realm of production, steel marking attracts attention as a precise and efficient method for forming metal sheets into various forms with amazing consistency. From the initial design phase where elaborate patterns take shape to the elaborate production processes, metal stamping is a mix of virtuosity and design. Diving right into this globe unveils an intricate interaction of creative thinking and technological proficiency, using a look into a realm where innovation satisfies workmanship.
Background of Steel Stamping
Steel stamping, a widely made use of production procedure today, has a rich history that goes back to old times (Metal Stamping). The origins of metal marking can be mapped to ancient civilizations such as the Egyptians, who utilized stamping techniques to adorn precious jewelry and accessories with complex designs. Over time, steel stamping progressed, with human beings like the Greeks and Romans utilizing it for creating coins and decorative items
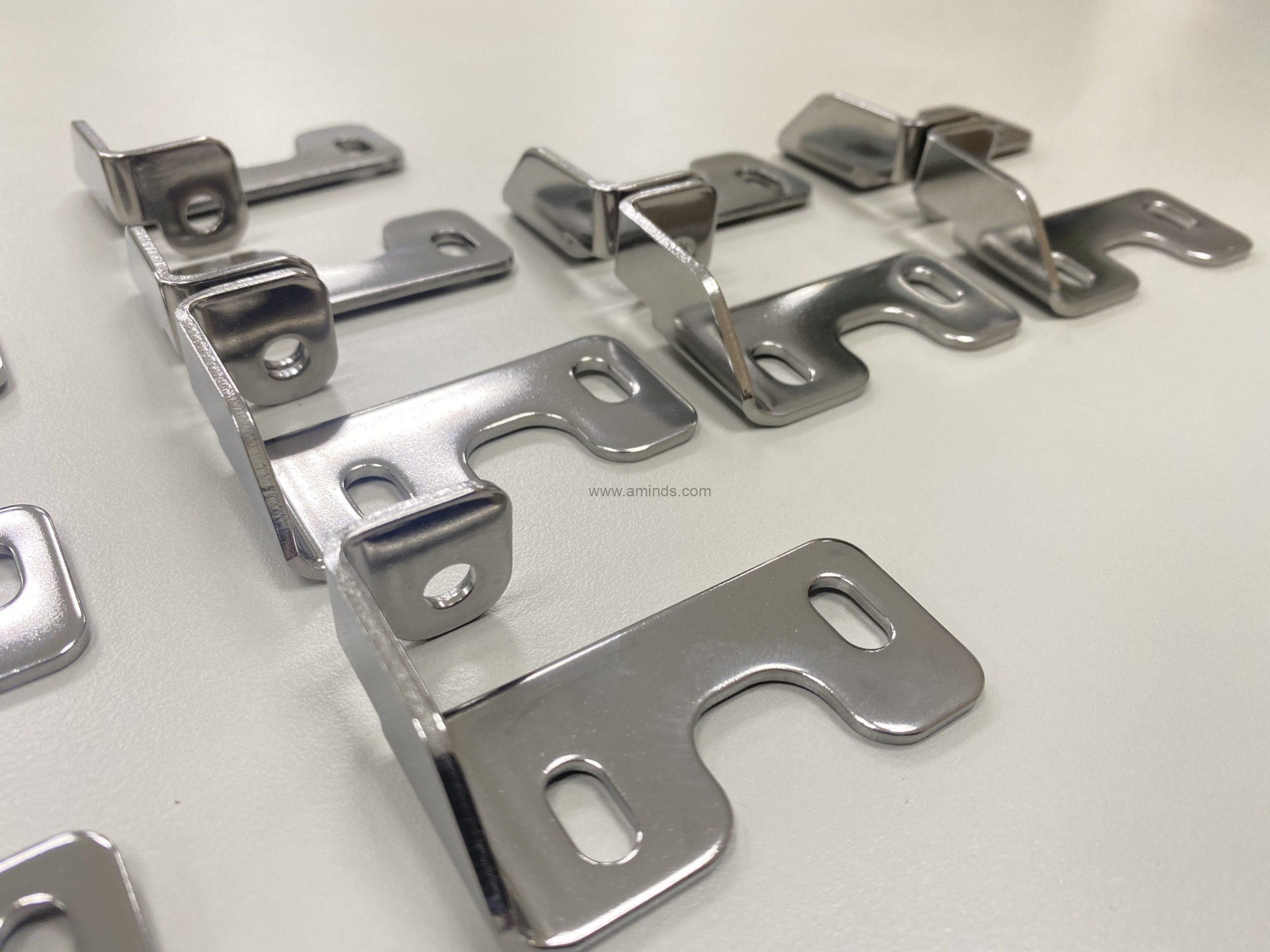
In the 20th century, steel stamping proceeded to develop with the assimilation of automation and computer mathematical control (CNC) technology. These advancements additionally enhanced the performance and precision of steel marking processes, making it an indispensable part of modern-day manufacturing throughout industries such as vehicle, aerospace, and electronics. Today, metal marking remains a crucial production process, integrating practice with development to fulfill the needs of a continuously advancing industry.
Style Factors To Consider and Prototyping
Layout factors to consider in steel marking consist of product choice, part geometry, tooling design, and production feasibility. Tooling layout plays a substantial duty in the success of steel marking jobs, impacting part accuracy, tool longevity, and manufacturing performance.
Prototyping is an important stage in the metal stamping process that permits designers to evaluate the style, verify manufacturability, and make required adjustments prior to major manufacturing. Prototyping aids determine potential problems at an early stage, saving time and prices over time. It additionally offers an opportunity to enhance the layout for performance and top quality. By meticulously thinking about style facets and using prototyping, manufacturers can improve the metal stamping procedure and achieve top notch, affordable manufacturing results.
Tooling and Equipment Basics
Taking into consideration the critical duty that tooling design plays in the success of metal marking tasks, recognizing the necessary devices and devices see this website needed is critical for achieving efficient production outcomes. Components hold the steel in location during the marking procedure, making sure accuracy and repeatability. Investing in high-quality tooling and tools not only enhances production efficiency yet additionally leads to higher precision, lowered waste, and general expense savings in steel marking operations.
Manufacturing Refine and Quality Assurance
Efficiently taking care of the production process and applying robust quality assurance actions are essential for making sure the success of metal marking projects. The production procedure in metal stamping involves a collection of steps that need to be very carefully coordinated to accomplish optimum results. It begins with the prep work of resources, adhered to by the setup of the marking devices and tooling. Operators after that feed the products into the press, where the stamping procedure occurs. Throughout this process, it is vital to check the manufacturing line for any kind of problems that might affect the high quality of the stamped components.
Quality control in metal marking is vital to provide products that fulfill the required requirements. By preserving rigorous high quality control standards, producers can support their track record for supplying high-grade metal marked items.
Applications and Market Insights
In the realm of steel marking, the effective application of production procedures and quality control steps directly affects the efficiency and dependability of numerous market applications and offers important insights right into the field's operational dynamics. Metal marking finds prevalent application throughout diverse markets, consisting of automotive, aerospace, electronic devices, and home appliances. In the automobile field, metal stamping plays a vital duty in creating elements such as check my site chassis, braces, and structural components with high precision and efficiency. The aerospace sector counts on metal marking for producing complex components like panels, braces, and fittings browse around this web-site that satisfy strict top quality standards (Metal Stamping). In the electronic devices sector, steel stamping is used to develop specific elements like adapters, terminals, and warmth sinks. In addition, steel stamping helps with the production of different family appliances, including refrigerators, cleaning machines, and ovens, by giving economical remedies for manufacturing resilient and complicated components. Understanding the applications and sector insights of metal stamping is vital for maximizing manufacturing procedures and enhancing product quality across different markets.
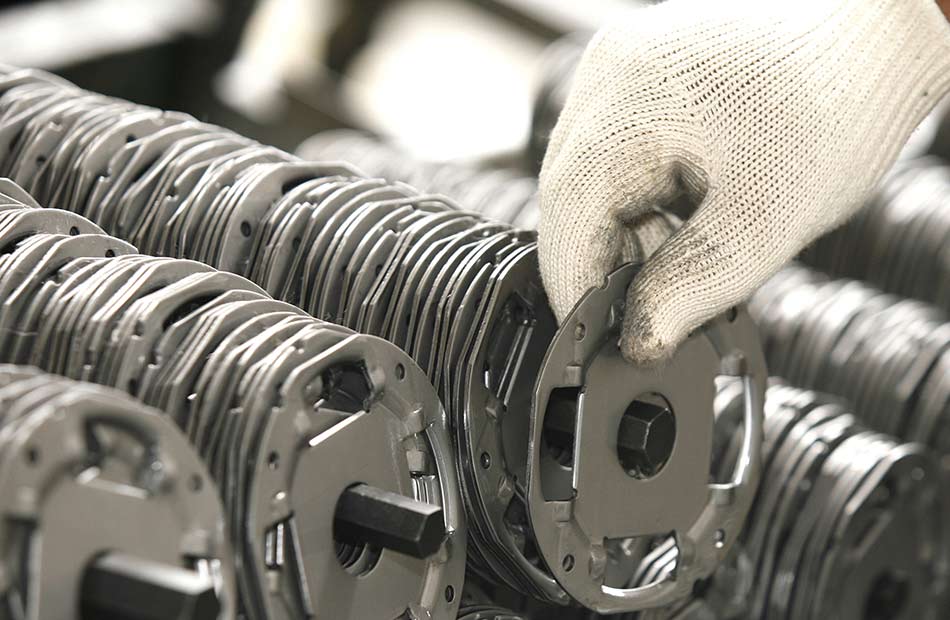
Verdict
Style factors to consider, prototyping, tooling, devices, manufacturing processes, and top quality control are necessary aspects of steel stamping. With its extensive applications and sector insights, steel marking continues to be a functional and reliable manufacturing procedure.